The six key value-adding functions of Fastems’ flexible automation
A pallet pool is an easy-to-buy, easy-to-implement automation solution for machine tools. It increases the lights-out manufacturing periods and machine tool utilization up to 65% – no wonder it’s such a popular option. That said, before investing in automation, it’s a good idea to evaluate not only the needs of today, but also the needs of tomorrow. That’s why in this post, we’ll share the six key value-adding functions of Fastems’ flexible automation. Keep reading to find out what we can do in addition to offering the same benefits as pallet pools.
1. Extendibility for more machines
The part mix rarely remains the same for years. These days, customers want more customized products at a faster pace, meaning that production needs to adapt quickly. With a pallet pool, you always need a new system with a new machine tool. In contrast, flexible automation can run multiple machine tools, and can be extended later on for future needs. Furthermore, in flexible automation all the machines and pallets operate under one control. This means one operator is able to run many machine tools, which in turn generates savings in both investment and operative costs.
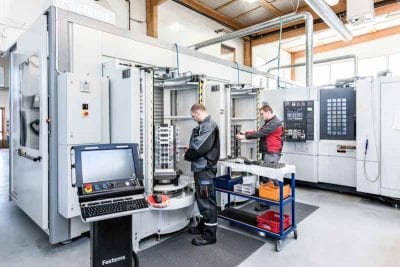
A Fastems flexible automation example from Kytola Instruments. Here, an FPC automated two existing machines, integrating two loading and unloading stations.
2.Pallet production order adapts to changes
When you load a pallet pool, you also fix the production order: pallet 1, pallet 2, pallet 3, and so on. In flexible automation however, the order in which pallets are to be machined is not fixed. The control of flexible automation, Manufacturing Management Software (MMS), constantly prioritizes the machining order of the pallets based on real-time customer orders. This ensures that every customer get their orders reliably and on time, even if an order has been placed last minute. In turn, this enables optimal machine utilization, combined with manufacturing the right parts at the right time.
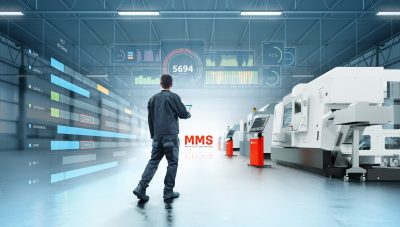
Fastems MMS constantly prioritizes the machining order of the pallets based on real-time customer orders.
3. Predictive production scheduling
MMS has real-time visibility over the entire production process. This includes orders and due dates, as well as machine tools and capacities. Different resources, like cutting tools, raw materials, fixtures and NC programs are also taken care of. MMS knows what needs to done and when, and what machines and resources will be needed. The control sends alerts about ‘to-be-missing’ resources in advance, so that operators have time to prepare them before the machine stops. Nevertheless, should a resource problem that cannot be fixed occur, MMS will re-do the production plan so that the second most important orders get done next. This is a drastic difference to typical pallet pools, and enables operators to eliminate hinderance, as well as small (and large) production stops.
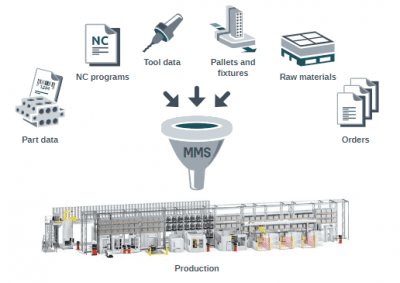
MMS has real-time visibility over the entire production process.
4. Higher pallet capacity with smaller footprint
In a pallet pool, the number of pallets used per machine is limited. In contrast, having a pallet storage with two to five levels allows flexible automation to store machining and material pallets in a very compact floorspace. The more machines (and pallet pools) you would need, the more space savings flexible automation can provide.
5. Maximize and ensure lights-out capacity and reliability
It’s true that pallet pools enable longer lights-out production times. That said, one pallet pool can run only one machine tool and has a smaller pallet capacity compared to flexible automation. As a result, flexible automation does not only multiply lights-out production times – it also makes sure there won’t be any unpleasant surprises during nights and weekends. This is because MMS instructs in advance which production resources need to be prepared before the manned shift ends. If something goes wrong, flexible automation makes sure the most critical work is still carried out.
6. Real-time production monitoring
With pallet pools, you only get information about one single machine tool’s utilization. With flexible automation however, you get real-time statuses and KPI reports of the overall production. This allows you to easily see how well your capacity is utilized and what the possible bottleneck resources are. In addition, you see how your performance indicators look like, enabling you to make continuous improvements in production.
A solution for even the simplest of productivity needs
All of the factors listed above make flexible automation a superseding option compared to pallet pools, even for the simplest of productivity needs. After all, keeping your options open for future expansions is increasingly important. Still not entirely convinced? Here are a couple stories about companies all over the world that have selected flexible automation over other standard automation solutions.
“The software doesn’t just run through pallets 1, 2, 3, 4, 5, etc., sequentially. It has intelligence; it looks at everything that needs to be manufactured and when jobs need to be done.”
– President of Mach Machine, using FMS ONE
“In the past we needed larger manufacturing batches for these machines to be productive. Now we can manufacture even very small batches very economically.”
– CEO, Kytola Instruments, using Flexible Pallet Container (FPC)
“We communicate the due date and the quantity required. Then MMS can ‘play chess’, look at the work that’s scheduled and come up with a plan that will meet the delivery dates, take advantage of the resources available, and maximize spindle time.”
– COO, Hirsh Precision Machining, using FMS ONE
Mach Machine Case Kytola Instruments Case Hirsh Precision Case