Imparare l’automazione flessibile alla velocità di un’auto da corsa
Nell’ambito del progetto interno “Formula 1”, la Cutmetall Recycling Tools Germany si è prefissata l’obiettivo di acquisire conoscenze pratiche sull’automazione in tempi record. I loro partner principali: Fastems, Heller e Haimer. L’obiettivo di questo progetto era sviluppare e testare nuovi standard di produzione, flussi di lavoro, attrezzature e programmi NC che potessero essere trasferiti direttamente in un sistema Fastems più grande entro il 2025. In questo modo, Cutmetall ha posto le basi per l’avviamento e sviluppo di un sistema di automazione multi-macchina rapido e a basso rischio.
Con sede a Eisfeld, in Turingia, Cutmetall Recycling Tools Germany fa parte del Gruppo Cutmetall e opera come OEM con circa 40 dipendenti. L’azienda produce pezzi di ricambio per l’industria del riciclo e per trituratori. “Produciamo lotti da 1 a 20.000 pezzi, anche se la media è tra i 20 e i 200 pezzi”, spiega l’amministratore delegato Florian Fischer.
Solo le ore di lavoro dei mandrini generano profitto
Fischer ha una visione molto precisa dell’automazione. Quando gli è stato chiesto come avrebbe valutato il livello di automazione del suo stabilimento prima del progetto “Formula 1”, la sua risposta è stata chiara: “Dipende da cosa si intende per automazione. Abbiamo dodici macchine CNC, un centro di taglio e tre robot per il carico e lo scarico delle macchine. Ad alcuni potrebbe sembrare un’automazione di alto livello, ma per me non lo è. Dal punto di vista del Lean Manufacturing, c’è ancora troppa poca distinzione tra creazione di valore e spreco. L’automazione non dovrebbe mai limitarsi a far funzionare le cose. Si tratta di massimizzare le ore di lavoro dei mandrini: è da lì che viene il profitto”.
Imparare velocemente dall’automazione reale
Secondo Fischer, la carenza di manodopera qualificata è il maggior limite alla capacità produttiva di Cutmetall. “Volevamo un’attrezzatura che potesse funzionare senza supervisione, e finora non avevamo nessun centro di lavoro orizzontale. Anche sulle macchine verticali, la rimozione dei trucioli è il principale collo di bottiglia, che rende difficile la produzione 24/7. Inoltre, le nostre macchine non avevano magazzini utensili sufficientemente grandi”.
Per cambiare questa situazione, Fischer e il comproprietario Oliver Huther hanno lanciato il progetto “Formula 1”, con l’ambizione di prepararsi a un futuro Multi-Level System (MLS) Fastems che avrebbe collegato più macchine CNC in un sistema di produzione flessibile. Il primo passo: implementare rapidamente una soluzione di automazione compatta e raccogliere preziose esperienze pratiche.
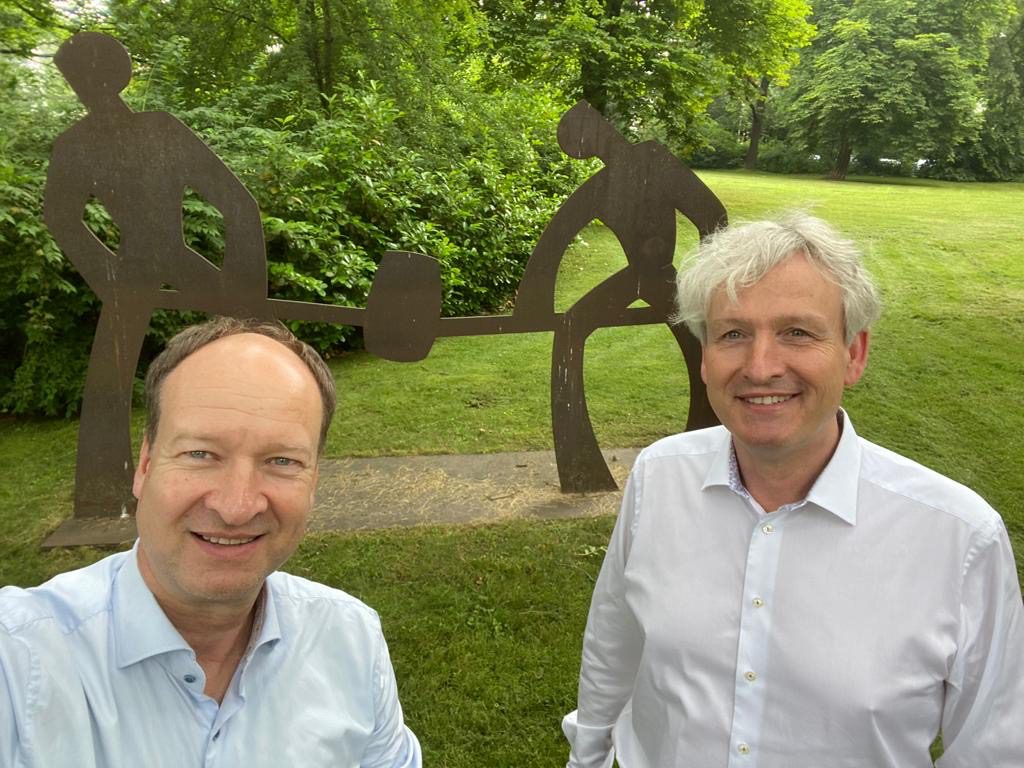
Gli standard prima di tutto: costruire le fondamenta per la produttività
Per sostenere questa transizione, Cutmetall ha iniziato a standardizzare sistematicamente il suo ambiente di produzione, come segue:
- Gli investimenti sono ora limitati a una uniformità di macchine con il medesimo controllo, modalità cambio pallet e sistemi di serraggio,
- Verranno utilizzati solo centri di lavoro orizzontali con rimozione automatica dei trucioli,
- Anche la gestione del refrigerante/lubrificante sarà automatizzata.
Fischer definisce l’obiettivo principale in questo modo: “Tutti i processi di impostazione, cambio, manipolazione degli utensili e rimozione dei trucioli devono avvenire in tempi mascherati”.
Per valutare i potenziali partner di automazione, Fischer ha visitato molte aziende della regione, con l’obiettivo di imparare dagli errori degli altri, prima di commetterne in prima persona.
Progressi rapidi: dalla fiera AMB al sistema produttivo
Cutmetall ha incontrato per la prima volta il centro di lavoro orizzontale a 5 assi HF 5500 di Heller alla AMB 2022. Allo stand Fastems ha scoperto il Flexible Pallet Tower (FPT), il pezzo mancante per completare la propria soluzione.
“Poco dopo la fiera, abbiamo acquistato il centro di lavoro direttamente dalla linea di produzione di Heller, insieme all’FPT-1000 di Fastems e a un dispositivo di preimpostazione di Haimer”, spiega Fischer. “Volevamo che l’intero sistema fosse operativo, completamente integrato e produttivo entro l’aprile dell’anno successivo”.
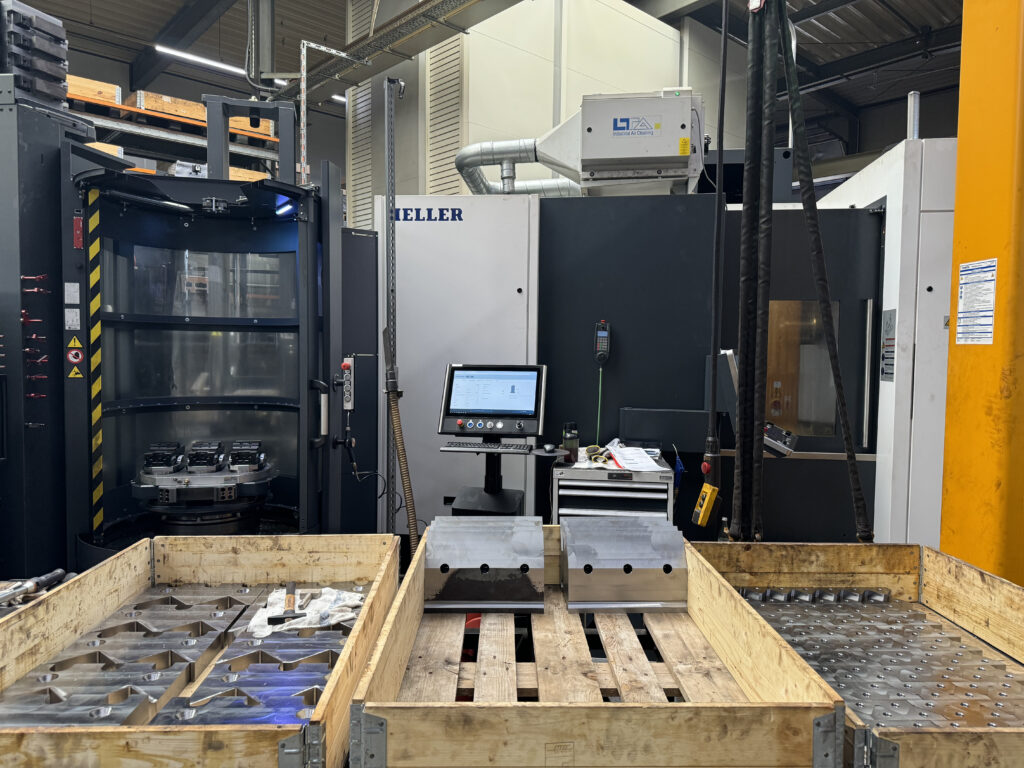
A convincere Fischer è stato soprattutto il concept di ottimizzazione dello spazio dell’FPT-1000, che consente un’elevata capacità di carico dei pallet in un ingombro ridotto. Progettato per carichi utili fino a 1.000 kg (pallet incluso) e pallet di dimensioni comprese tra 500×500 mm e 630×630 mm, il sistema può immagazzinare 12-24 pallet in due livelli di altezza, il tutto in soli 19 mq di superficie. Questa configurazione supporta una produzione altamente efficiente e orientata agli ordini con un’unica macchina CNC.
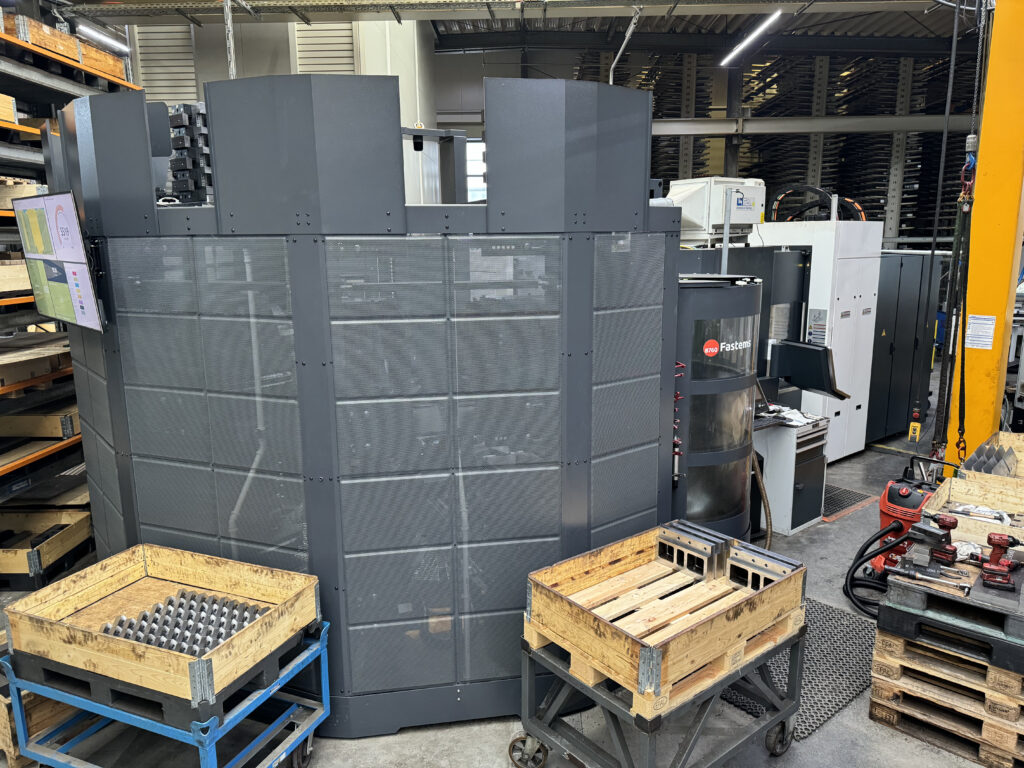
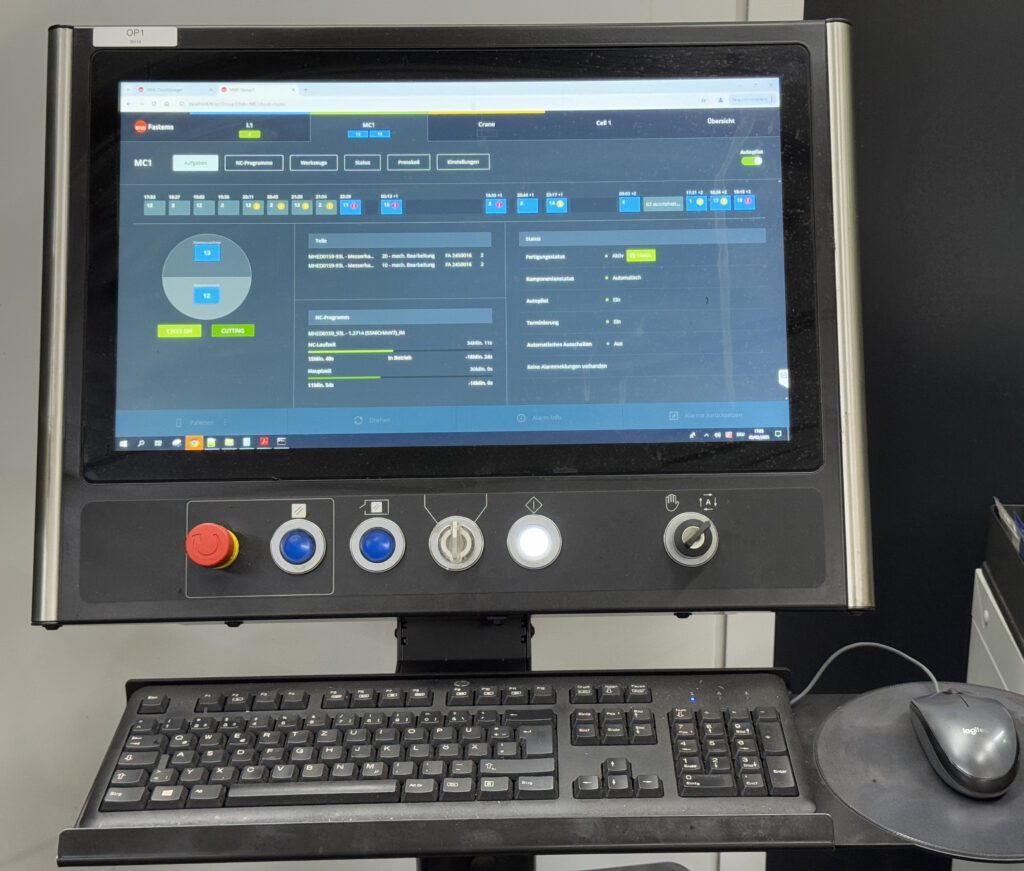
Il software fa la differenza
Per Fischer, non è stato solo l’hardware a suggellare l’accordo, ma l’integrazione complessiva del sistema, in particolare il software. “Le interfacce software tra la macchina, il dispositivo di pre-setting e l’automazione sono assolutamente fondamentali. L’MMS (Manufacturing Management Software) di Fastems ha fatto pendere la bilancia a favore di Fastems”.
L’MMS è una delle soluzioni software più avanzate per la pianificazione, l’esecuzione e il monitoraggio della produzione. Può programmare le operazioni di produzione fino a 96 ore prima. Soprattutto, si concentra sulla preparazione delle risorse: “Prima di avviare un lavoro, l’MMS verifica la disponibilità dei materiali, i programmi NC, gli utensili (compresa la durata residua), le attrezzature e altro ancora. Solo quando è tutto pronto, il sistema inizia la produzione. Di conseguenza, abbiamo molti meno pezzi in attesa tra un’operazione e l’altra”.
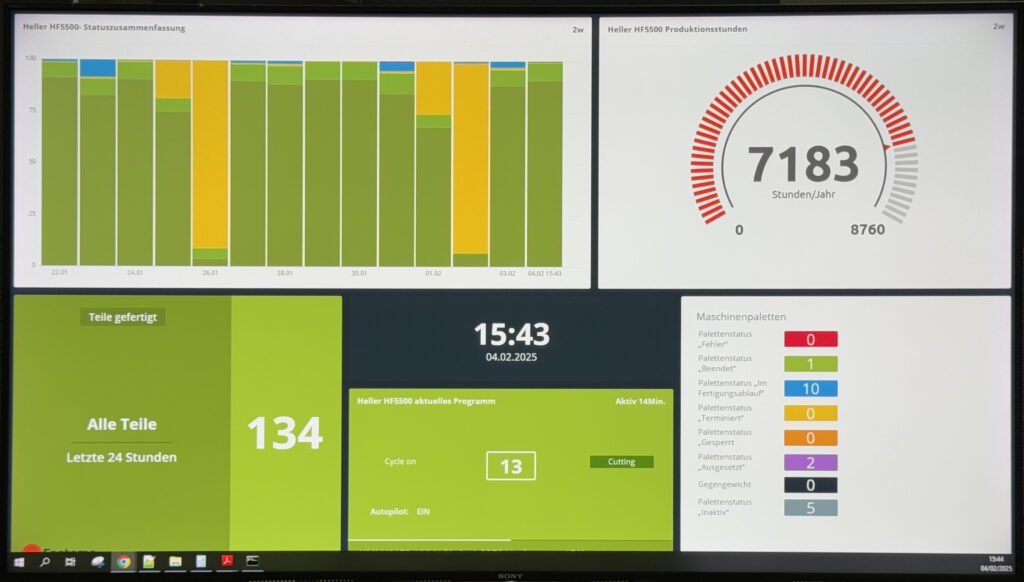
Risorse produttive gestite centralmente
Una volta memorizzati i dati dei pezzi nell’MMS, gli ordini ripetuti possono essere avviati immediatamente. “Ci fa risparmiare moltissimo tempo, a patto che le materie prime, i pallet e gli utensili siano pronti”, spiega Fischer. “L’MMS si occupa anche della gestione completa degli utensili e invia le istruzioni all’unità di pre-setting. In questo modo, tutte le nostre risorse produttive critiche sono gestite centralmente”.
E aggiunge: “Sì, il software non taglia il metallo, ma aumenta in modo significativo le ore di lavoro dei mandrini. Ogni minuto in cui una macchina non produce trucioli è uno spreco”.
Attualmente, gli ordini di produzione vengono ancora inseriti manualmente nel controllo. Ma con la futura integrazione di MMS nel sistema ERP, i 20 dipendenti del team “Fomula 1” stanno già acquisendo una preziosa esperienza pratica con il software e le sue potenzialità.
Mantenere il flusso dei pezzi con l’FPT-1000
Oggi, l’FPT-1000 di Cutmetall contiene 18 pallet di diverse altezze. Le attrezzature rimangono sui pallet della macchina e ogni pallet contiene in genere un solo tipo di pezzo. Dopo l’OP10, i pezzi vengono ricollocati sullo stesso pallet per l’OP20.
“Quando un pallet esce dall’FPT, abbiamo sempre un mix di pezzi finiti, pezzi grezzi pronti per l’OP10 e pezzi bloccati per l’OP20”, spiega Fischer. “I tempi di lavorazione dei pallet variano da 30 a 90 minuti”.
L’impianto funziona su due turni al giorno, con un ulteriore turno notturno non presidiato. A supporto di ciò, Cutmetall sta progettando di trasferire automaticamente i trucioli da tutte le macchine a un convogliatore centrale.
Obiettivi ambiziosi, per definire con chiarezza i prossimi passi
Con il progetto “Fomula 1”, Cutmetall ha già raggiunto i propri obiettivi iniziali: acquisire esperienza pratica di automazione, sviluppare conoscenze interne e prepararsi al livello successivo.
Grazie alla soluzione FPT-1000, l’azienda raggiunge attualmente oltre 7.000 ore di automazione all’anno, di cui il 90% sono ore effettive di mandrino e solo il 10% è utilizzato per il cambio pallet e utensili.
“Per un’azienda di medie dimensioni come la nostra, con lotti relativamente piccoli, gli investimenti importanti devono ripagare. Il fatto che ora possiamo ammortizzare una macchina su oltre 7.000 ore produttive all’anno è un grande successo”.