Come USNR ha ristrutturato i suoi impianti per la massima efficienza
Article & Photos Supplied by Mary Ellen Klukow, Editorial Associate – Lynn Gorman Communications LLC
- Informazioni sull’azienda: USNR è il produttore numero 1 al mondo di attrezzature per l’industria della lavorazione del legno, con 11 stabilimenti in Nord America e otto in Europa e Asia. La loro sede globale è a Woodland, Washington, sede di un officina in crescita di 100.000 piedi quadrati che produce parti come molatrici e seghe a nastro.
- Problema: “In precedenza, la maggior parte dei pezzi veniva realizzata su centri di lavorazione verticali, il che significava che i mandrini erano inattivi mentre gli operatori cambiavano pezzi, attrezzature e utensili. Insieme a questo lento processo, non c’erano utensili residenti in nessuna delle macchine per ridurre al minimo la configurazione. Il nuovo metodo mantiene i mandrini di USNR il più attivi possibile. La configurazione viene eseguita offline e ogni macchina dispone di utensili residenti e identici per eliminare i colli di bottiglia “.
- Soluzione: per sostituire i centri di lavoro verticali, Fastems ha fornito il loro sistema di produzione flessibile (FMS) e tre nuovi centri di lavoro orizzontali DMG / MORI NHX 6300. L’FMS è stato fornito come parte del pacchetto FMS ONE.
- Risultati: USNR è riuscita a ridurre i tempi medi di consegna da 25 a nove giorni. “Abbiamo anche finito il lavoro per quello che avevamo programmato. Ho avvertito tutti: “masticherà tutto il lavoro. Soprattutto le cose che sono già state dimostrate “, ha affermato Mike Smothers, responsabile delle operazioni.
USNR è il leader mondiale nella produzione di attrezzature per le industrie di segheria e lavorazione del legno, fornendo parti in Nord America, Sud America, Europa, Asia, Australia e Nuova Zelanda. Mike Smothers, direttore delle operazioni, chiama l’officinaUSNR a Woodland, Washington, una struttura “high mix, low volume”. Uno stabilimento di 100.000 piedi quadrati evade gli ordini di molatrici, profilatrici, cippatrici, seghe a nastro e altre parti specializzate per le industrie di segheria e pannelli, con pochi articoli prodotti a volumi molto più elevati.
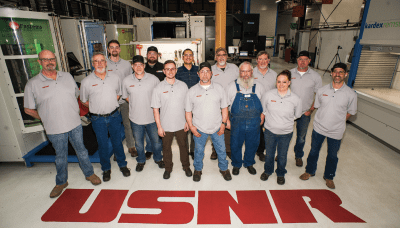
Woodland dell’USNR, il team di Washington FMS e i membri di supporto.
Quando Smothers è stato assunto, una delle prime modifiche che ha apportato è stata l’installazione di un Fastems Flexible Manufacturing System (FMS). L’FMS include tre centri di lavoro orizzontali DMG / MORI NHX 6300 e organizza e pianifica i progetti per massimizzare la produttività. In precedenza, la maggior parte dei pezzi veniva realizzata su centri di lavoro verticali, il che significava che i mandrini erano inattivi mentre gli operatori stavano cambiando pezzi, attrezzature e utensili. Insieme a questo lento processo, non c’erano utensili residenti in nessuna delle macchine per ridurre al minimo la configurazione. Il nuovo metodo mantiene i mandrini di USNR il più attivi possibile. La configurazione viene eseguita offline e ogni macchina dispone di strumenti residenti e identici per eliminare i colli di bottiglia.
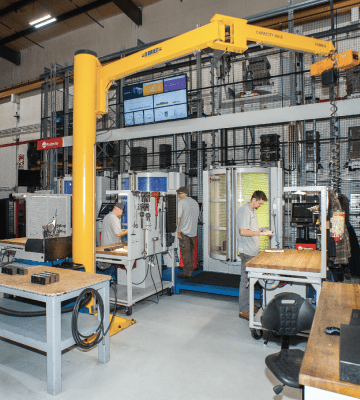
Lo stabilimento di USNR è suddiviso in celle di produzione, in cui può svolgersi l’intero processo di produzione di un pezzo.
Anche i quattro stabilimenti USNR (Woodland, WA, Jacksonville, FL, Plessisville, QC e Söderhamn, Svezia) stanno adottando un sistema UPS [USNR Production System]. La premessa di questo sistema è di consentire all’officina di aumentare la velocità e abbassare i livelli di WIP (Work in Process) per consentire all’azienda di spostare rapidamente il materiale attraverso i negozi. Uno dei suoi obiettivi con questo sistema è ridurre il tempo medio di consegna di USNR a cinque giorni.
“Woodland era a 25 giorni e ora siamo scesi a una media di 9 giorni e stiamo lavorando verso i 5 giorni”, spiega Smothers. “Raggiungere i 10 giorni è stato un grande traguardo per il nostro nstabilimento e il sistema UPS, ora stiamo lavorando su una media di 5 giorni.”
Il sistema UPS va oltre la programmazione per realizzare l’organizzazione fisica. Due moduli di sollevamento verticale Kardex Remstar mantengono ordinati i materiali, le parti e le attrezzature di USNR. “Il mio magazzino è in quelle due macchine Kardex. Mantiene tutto in vassoi e registra dove tutto è. Piuttosto che avere una persona che cammina intorno a ciascuno degli scaffali nelle aree di rifornimento, al piano di sopra e al piano di sotto, l’operatore si trova vicino all’apertura simile alla porta del garage e il sistema consegna gli articoli direttamente a quell’apertura. ” I moduli riorganizzano settimanalmente i loro vassoi in modo che le parti utilizzate più di frequente siano più vicine alle aperture, snellendo ulteriormente il processo. Soprattutto, possono essere integrati con il sistema FMS e posizionati nella configurazione cellulare.
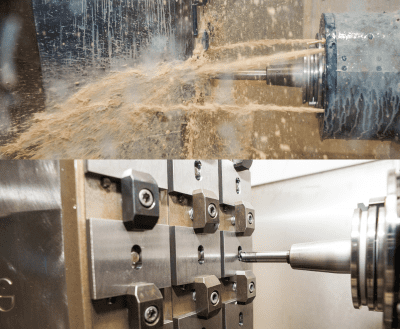
L’utilizzo di tre stazioni di carico nell’FMS massimizza il tempo impiegato per la lavorazione nei tre centri di lavoro orizzontali NHX6300 invece di abbattere e montare i pezzi nelle macchine orientate in verticale, come i centri di lavoro verticali.
Smothers ha anche ristrutturato il resto della fabbrica in celle di produzione. “La nostra officina era originariamente organizzata in gruppi: tutti i mulini qui, tutti i trapani lì, tutti i trapani a colonna dall’altra parte e così via. Lo stiamo demolendo e produciamo celle come parte del nostro sistema UPS “, afferma Smothers. Queste celle di produzione sono configurate in modo che quasi tutto per una parte possa essere fatto in un’unica posizione. Man mano che i lavori vengono ricevuti ed elaborati, i coordinatori dell’officina mettono in scena il materiale e spostano le parti in celle diverse in modo che gli operatori possano concentrarsi sulle parti designate. “Una persona segue completamente il lavoro. Stiamo enfatizzando la qualità e la velocità: ricevere gli ordini in entrata e in uscita rapidamente e correttamente “.
Per ottenere ciò, Smothers ha introdotto macchine CNC come frese/torni. “L’intera idea di macchine come questa è ‘tutto in uno‘. Vogliamo mettere la materia prima nella macchina e far uscire un pezzo finito. Con macchine autonome il materiale andrebbe a un tornio, quindi in una fresa e così via. Ora le parti sono completamente lavorate su questa macchina.”
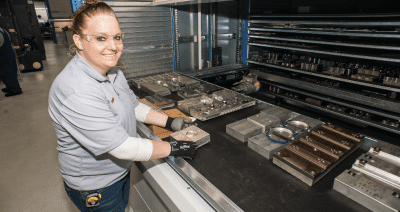
Kasi Larson, coordinatore dell’officina meccanica, utilizza le unità Kardex Remstar per immagazzinare parti, dispositivi e strumenti.
Smothers ha anche scoperto che uno dei modi migliori per aumentare l’efficienza è che gli operatori facciano funzionare le loro macchine senza sorveglianza. All’inizio molti operatori dell’USNR erano interessati a questa prospettiva; alcune delle loro parti hanno tolleranze entro due o tre decimillesimi di pollice. Ecco perché Smothers ha enfatizzato prima di tutto provare i modelli.
Il programmatore CNC Adam Corson lo fa portando un modello 3D nel software CAD / CAM Mastercam da programmare. Corson ha programmato con questo software dal 2007. Ha spiegato: “Ha molte opzioni che semplificano il mio lavoro, sia che si tratti di un percorso utensile dinamico che ci consente di ottenere il taglio a tutta lunghezza della scanalatura utilizzando velocità del mandrino più elevate e velocità di avanzamento più veloci, fino a superfici con forme particolari che ci consentono di utilizzare i nostri centri di lavoro CNC al massimo delle loro capacità. ” USNR trova il massimo valore nel modo in cui il software ispira fiducia negli operatori.
Le potenti funzionalità di simulazione all’interno del software sono essenziali. Con il backplot e le funzioni di verifica, Corson può verificare la presenza di errori e possibili problemi di lavorazione su uno schermo intuitivo che modella il processo di lavorazione effettivo. Quindi condivide queste informazioni con gli operatori. “Manipoliamo il nostro modello per rappresentare esattamente ciò che l’operatore vedrà nella macchina. I nostri operatori hanno la capacità di visualizzare il modello sulla loro stazione di lavoro, il che fornisce loro la migliore comprensione di cosa aspettarsi dal programma “. Tra l’aver provato il codice e la visione del modello sui propri schermi, gli operatori si sentono a proprio agio a far funzionare le loro macchine a luci spente.
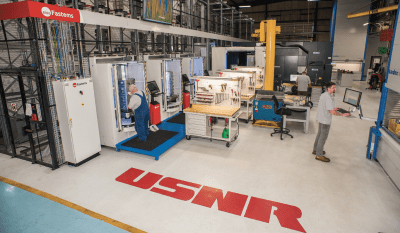
Lo stabilimento USNR di Woodland, Washington, si affida a un Fastems FMS per migliorare la velocità, la precisione e i tempi di consegna della produzione dei pezzi.
Corson ha spiegato che trovare il software giusto è fondamentale per l’efficienza di una officina, sia per la programmazione che per la pianificazione e l’organizzazione. “Il sistema Fastems è stato un punto di svolta per averci aiutato a far entrare e uscire le parti dalle macchine con il minor tempo possibile di gestione del materiale. La materia prima, una volta caricata su un dispositivo, andrà automaticamente in uno dei tre HMC collegati al sistema Fastems. Essere in grado di gestire la vita utensile su 990 portautensili e tutti i 54 pallet da una singola stazione di carico ha reso i nostri processi molto più prevedibili e più sicuri per tutti i nostri operatori “. Il software di gestione della produzione (MMS) di Fastems fa parte del pacchetto FMS ONE ed è progettato per mantenere un’officina fluida. Una volta che gli operatori hanno configurato la parte e l’attrezzatura, comunicano a Fastems che è stata caricata. Fastems lo pianificherà e ci comunicherà sul tabellone, ad esempio, che l’utensile 35 MC1 numero macchina deve essere cambiato. Si assicura che tutto sia aggiornato e che continui a funzionare. Fastems si occupa di tutto ciò che ha a che fare con il funzionamento della cella. ” Smothers spiega che anche se questo stabilimento utilizza un pacchetto standard, l’equipaggio di Fastems è stato più che felice di aiutarlo a trovare soluzioni personalizzate in altre officine con cui ha lavorato in passato.
Smothers sapeva di aspettarsi maggiori risparmi quando incorporò l’FMS, riorganizzò il layout delle celle e rese possibile la produzione a luci spente. Quello che non si aspettava era quanto l’USNR avrebbe risparmiato.
“Abbiamo anche finito il lavoro per quello che avevamo programmato. Ho avvertito tutti: “masticherà tutto il lavoro. Soprattutto le cose che sono già state provate. ”
Mentre USNR aumenta la sua produttività, Smothers mantiene il suo obiettivo di ridurre i tempi medi di consegna a cinque giorni o meno. “Vorremmo arrivare al punto in cui quando un cliente chiama ho la materia prima pronta, la metto nella macchina, la metto in funzione e la spedisco lo stesso giorno.” Gran parte del processo è automatizzato ora e pensa che il raggiungimento di questo obiettivo sarà possibile in un futuro molto prossimo.
Originale pubblicato su CNC-West
Maggiori informazioni su FMS One Maggiori informazioni su MMS